
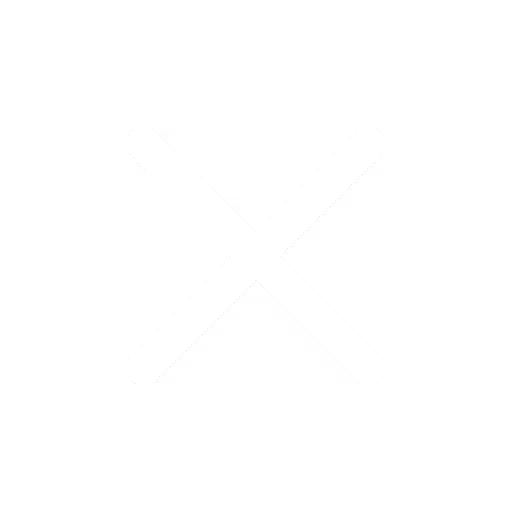
Vapor Recovery

Methane Leak Detection

Production Optimization

Integrated Capabilities

Sustainability

About

Careers

Contact Us

Methane Leak Detection

Product Optimization

Integrated Capabilities

Sustainability

Knowledge Center

Join Ali Sylvester, Director of Business Solutions, and Aaron Baker, VP of Compressor Engineering at Flogistix, as they explore the latest innovations in vapor recovery with the new VRX series. In this episode, they discuss how the VRX 7, VRX 15, and VRX 25 vapor recovery units (VRUs) are designed to meet today's emissions control demands while providing cost-effective solutions for small-scale applications. Learn how these compact units tackle regulatory challenges and deliver optimized performance for marginal wells.
Don’t miss expert insights into the evolving vapor recovery landscape and how Flogistix is leading the way in vru engineering.
Learn more:
Vapor Recovery FAQs
What is Vapor Recovery?
The Benefits of Vapor Recovery
The Vapor Recovery Process
Ali
Welcome back to Fueling Conversation. I'm Ali Sylvester, Director of Business Solutions. Today, I'm joined by Aaron Baker, Vice President of Compressor Engineering at Flogistix. Thanks for joining us, Aaron.
Aaron
Thanks, Ali. I'm very excited about this. I was thinking about the podcast thing in general. I love to talk shop.
I talk with a lot of people and I'm really interested to see who we reach out to here, who accesses this. Hope we, hope we draw a large Audience because there's so many conversations that we have all the time that are really important and relevant. And I would go speak with everybody I could about it if we had time. It sounds tiring, but there's just lots of things to say about our industry. And this is going to be a fantastic way to get that news out. So I'm really happy about this.
Ali
So, what are some of the most exciting things that you do want to talk about?
Aaron
Well, we've got a lot going on, you know, we're growing fast, we, we try to innovate and the world is very different.
The last few years, the focus on emissions control and, and our solution really plugs well into that. Everything that we do in that direction I think is very exciting, I want to talk about it. Especially today, I really want to talk about some of our new, smaller machines, our VRX series, particularly our VRX 7.
I think to start that out though, I need to talk more general about vapor recovery. We've got a lot of machines, and I know that it's been said that it's a vapor recovery unit. Really, vapor recovery is an application, and these are gas compressors. But the wells that we apply these on are different. So there's a facility and sometimes there's a lot of wells.
Maybe, maybe 10, 15 wells. There's a lot of things going on. And these, these wells are usually oil and gas. So there's liquids and gas coming out of it. But they're big and there's, there's more production and we do bigger and bigger units. So that's, that's kind of been the trend is vapor recovery is just becoming a larger segment of the whole energy industry.
And so we go and take care of this. We also have smaller machines, but the interesting thing now is that as we progress as a, as an industry and a nation, we get better at handling these emissions and our Interests continue to get sharper and sharper. So we have more opportunity todo what we do well, what we've done for a long time in these big units down on smaller scales.
Now, there's always been vapor recovery for these little bitty machines and these little applications, but it's viewed differently. There's some pretty simple and inexpensive pieces of equipment out there that they just kind of turn on and turn off as needed. They, they work okay, but they, they don't do the really detailed control that's our forte and our niche.
And with the new mindset that the world has these days where every little bit of emissions matters, the focus on performance and just the quality of execution and, and our, and it's really a service, right? We rent equipment, but we optimize and, you know, we commissioned these things and we go out there and do vapor recovery as a service.
It's difficult to do that level of service at this kind of higher level, if you will, of execution and make it make economic sense. But there's so much more than just capturing the gas to it from an economic standpoint. You know, there's potential for carbon credits, there's penalties for venting and flaring, and there's more than just the value of the gas that we recover.
So that's driven. Our innovation and our development of products bigger for these bigger facilities, but also smaller. So we take our big stuff and our things that we do well, and we now have a new opportunity to put that into a smaller scope and a smaller scale. I think that's very interesting for our clients.
They've been struggling with a lot of these small machines that, you know, they are what they are. They start and they stop. They kind of have their niche, but we haven't been able to compete and join in that segment because of cost.
Ali
So, same tailored solutions, but different than the FX series that we would typically deploy. So, how is this VRX different than the FX series?
Aaron
Right. So, we have to really think differently about how we get these features and these tools that we have on a smaller scale and make it make sense. These things are just expensive, right? We have a lot of very high quality components. There's a lot of control equipment on there and we have to get super efficient in how we execute and build and use these things.
And that's what the VRX7 and it's, well, the whole family of VRX units, the VRX series is about. Our FX series is the fully featured range of our units. They have all the bells and whistles. They do all the things in vapor recovery. They do very, very well, but they are a bit overkill for some applications.
They've got features that you don't necessarily need everywhere. So we, we sought to build something extremely purpose driven for vapor recovery and the FX series designates these fully featured Flogistix units. But the VRX series. Designates the machines that are geared for vapor recovery. That's what the VR stands for.
We have to take some concessions, like we don't need a very large suction scrubber. Because we don't anticipate slugs of liquid. That's a wellhead type application. So we have a more appropriately sized for vapor recovery inlet vessel. There's just some other features that focus on vapor recovery, and it's kind of everything you need and nothing you don't.
So the Vape Recovery Series, the VRX Series, gives us this option to build something that's small and matches these marginal well applications that has just enough gas to put them on the radar for emissions, but makes it very difficult from an economic standpoint. We can build them in mass. We have a really unique design for this that allows us to get a lot more efficient, especially in batches, and we want to price it in batches too and give people the opportunity to go out and solve a lot of issues and make it the most efficient economic approach that they can.
It's just taking a step back from our standard designs, our standard approach, and thinking, you know, what are we doing that's unnecessary? What could we do differently that's better? And the VRX 7 is a 7.5 horsepower machine. It's only good for about 15 MCF, a very low volume. But it's ideal for those very low volume, single well, marginal well applications.
We take the same approach with the VRX 15. We've had this machine VRX 15 for a while and we've reimagined it and gotten our cost quite a bit down on it, making it in the same fashion that this new VRX 7 is. And then where it sort of transitions into the big boy unit, if you will, is what was the FX 8.
This is a 25 horsepower unit. It's being redesigned and reimagined as the VRX 25. So now we have the VRX 7. VRX 15 and VRX 25, three different horsepower category machines. It's a vapor recovery unit, we're talking about 15 mcf and about 40, 45 mcf and about 70 or 75 mcf with the three sizes. From there, we go up to the FX series and we have the ability to do higher pressures and more things.
But the VRX family is just for vapor recovery and just for those really tough applications from an economic perspective.
Ali
So you've talked a lot about the economics. What kind of design changes did you make to balance the cost while maintaining the high integrity of performance?
Aaron
One of the big things is a really unique vessel, a pressure vessel.
So pressure vessels are a big cost and we're an ASME code welding shop, so we do things right and doing things right has some expense to it. Well, if we can take one out, that's a big deal. So we built a special vessel that is a combination inlet scrubber, a very effective one. It's got a vane pack in it.
It does what it needs to do. It's got heat trace, just doesn't have a lot of volume because it's not meant to catch a slug. But it also is integrated with the discharge separator. And the discharge separator is super important for a rotary screw. There's oil that gets injected, And when the gas is discharged out of that compressor, it's a foamy mixture.
It's an oil and gas foam. Well, that oil is very expensive. That's a very special part of what we do with the screw and making it work in vapor recovery. So this vessel has a job, and that's to separate the oil and keep it in the unit. There's sizing and just general design aspects that all of the lessons learned from many years of doing screw compression and vapor recovery goes into this
So we have a really neat combination vessel. It has a small footprint. It's not much more difficult to build than a single small vessel. It's got a couple of internal things that are different. But we can build it pretty quickly and easily. And that's a major factor in the design. It's also small enough that in lieu of welded piping, we can do bent instrument tubing.
So there's oil circuits that is just bent tubing. There's even gas that's just bent tubing. We can get this thing down to where we're not even doing welded process piping. So in a manufacturing perspective, whether it's an assembly line, where you're moving the machines, or you're moving the specialists that are building it, you know, people welding, people assembling things, torquing bolts, that kind of thing, the work content breaks up nicely, called tack time, like we were doing this in this station and something else in another station, so we can, we can organize that to flow well.
But it's very, very low. There's only six things that weld to the skid and they, it's, it's structural, right? And all three of these units are the exact same vessel, exact same skid, exact same cooler. There's only a difference in the motor and the compressor. And they even bolt together, there's no alignment.
We could even build them where they're 90 percent complete. In the fab standpoint and then decide which version of the three we want to execute and finish. It makes things so much easier when we do the same activity over and over in large batches and lumping three different size machines into the same activity has tremendous benefits from an efficiency standpoint.
We of course pass that along to our customers. The sharper we can get our pencil, the better the offering, the better the value proposition we have for them.
Ali
Smaller unit, faster to build, more inventory to deploy, which this sounds great because as we mentioned in the last episode, the methane rule was just released on March8th.
So how might this new design solve the concerns for those impacted by the methane rule?
Aaron: Well, you could say it's timely for us to come out with this machine right now, but I can't ignore the fact that that's a lot of the driving force behind this is trying to keep up with the regulations and understand what our customers are really going to be faced with and what they need.
There's a tremendous amount of concern over retrofitting facilities and just handling these new rules, and what are they going to do about it? So we need to have the equipment ready. We need to be able to quickly build and deploy and satisfy that need. But there's actually small features in the unit that stem from this as well.
And this, this really goes throughout all of the FX Series units. Understanding more about what our customers are faced with and providing those detailed solutions. And this machine, the VRX series, has a electric scrubber pump. And that's typically an upgrade option. It's kind of a significant thing to get rid of the pneumatics to use this pump.
And we, from the get go, said let's just make that, this thing's an environmental solution. And we might as well use the environmental solution options where we can. It also is easily connected to instrument air for the recycle system. We could upgrade to a fully electronic recycle system. We have a couple of options there.
But this one is an easy way for us to handle everything that the new regulations are throwing at it. Down from the little details up to the quickly what do we need to get out and deploy to keep our customers incompliance and operating. They're going to be faced with the choice of shutting in, plugging, and abandoning a lot of these small wells.
And so the economics again come into play, but it needs to also be a simple solution. Vapor recovery is a difficult thing. You know, 15 years ago when we started doing this, it was, it was treated like an after thought. And we really pushed hard the economics of this. You guys are venting and flaring and we'd like to help you recover that gas.
It's worth a lot of money. And they knew that. It was a drop in the bucket compared to the oil, but it was such a challenge. The facilities weren't designed for it and they had a hard time executing it and making it work. The regulations forced them to, you know, address it and deal with it. But the fact that we've always been there and trying to help them make it work has gotten us into part of their, their solution, part of their design.
So vapor recovery is just an integral part of that life. And now that we have the VRX7, when they're going to go back and revisit wells that are formerly not being considered or handled this way, it gives them something pretty easy to retrofit. So it's just a simple solution, it's lightweight, easy to set, easy to move.
Ali
So then where should someone go to find out more about the VRX series?
Aaron
Well, first and foremost, I would speak with your local sales rep and our, our guys need to be able to answer these questions, get it through the applications engineering department, get a quote in hand. We can do that stuff quickly. We have all the drawings that they would need.
We have, uh, you know, 3d models if they need to plug that into their facility. It's just like our big machines are, we are fully featured and that includes the service, the support, the technical support. So for sure, start with the sales guys. We have some information on the website. Our field service mechanics are rapidly becoming familiar with these, we're sort of training and making them aware of it as well.
Any Flogistix contact, we'd want them to be able to direct them to answers.
Ali
That concludes today's episode of Fueling Conversation. Thank you to our listeners for joining us as Aaron Baker, Vice President of Compressor Engineering at Flogistix, shared invaluable insights into vapor recovery units in the new VRX series.
You can stay connected with us through our social media channels @Flogistix or delve deeper into our website, Flogistix.com. And if you have any thoughts, questions, or suggestions for future episodes, we'd love to hear from you. Feel free to reach out via email or social media. Until next time, take care.